Business Overview
Shanghai Turbo is a precision engineering group that specialises in the production of precision vane products, namely stationary vanes, moving vanes and nozzles. These vanes are the key components of steam turbine generators used for power generation in power plants, power stations and/or substations. They are also essential components mounted onto steam turbine generators to maximise the efficiency of steam flow in the generation of electricity.
Below is an overview of our company’s operations.
Raw Materials and Inspection
Special-grade alloy steel is the main raw material used in our manufacturing of vane products. The procurement of this raw material, and selection of suppliers, is carried out in accordance with strict quality control standards. The alloy steel is received either in the form of steel bars or semi-finished products that are already in the rough shape of the vane. Upon delivery, our inspectors conduct rigorous checks to ensure that the steel meets our requirements.
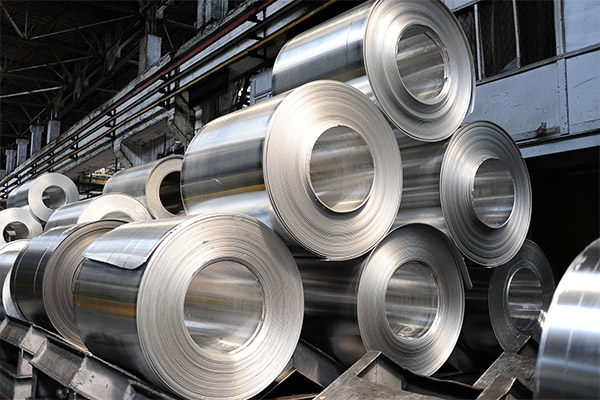
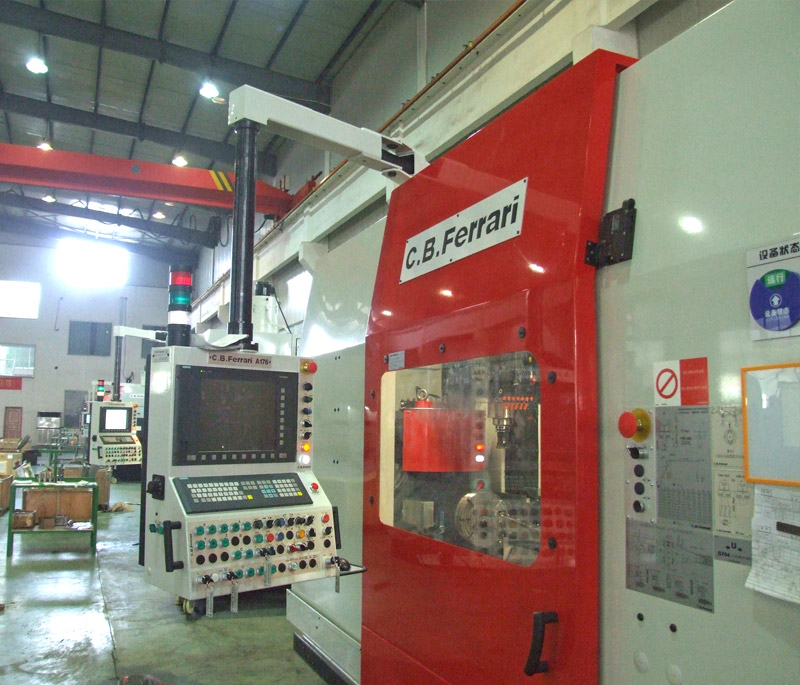
Precision Machining and Finishing
Based on the given specifications and drawings, the materials go through one or more key processes such as grinding, milling, and turning. As each machining process requires a high degree of dimensional accuracy, we have computer numerical controlled (CNC) precision machinery imported from Japan, Germany, Switzerland and Korea, and our machines are periodically upgraded and replaced to maintain the technological edge.
After completing the precision machining process, the semi-finished vane products will undergo the burnishing process where sharp edges and burrs on work pieces are removed. The entire surface is then polished using a polishing machine to ensure a smooth finish. Prior to completion, the products are cleaned and covered with a layer of protective coating to improve their corrosion resistance.
Quality Assurance
All quality inspection procedures are carried out by our quality assurance department, which is well-equipped with measuring gauges, height gauges, micrometers, and coordinate measuring machines. All our measuring equipment used to perform quality control and inspections are periodically calibrated against the master gauge blocks which comply with international standards.
All of our production parts are subject individually to first-piece inspection before mass production commences. The completed vane products are inspected and tested to ensure that their quality and properties are in accordance with our customers’ specifications prior to delivery.
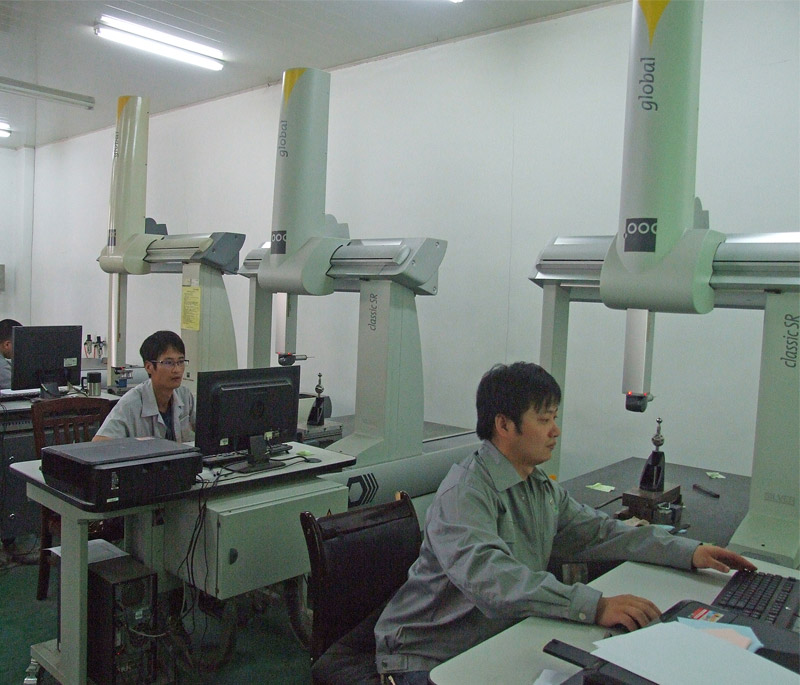
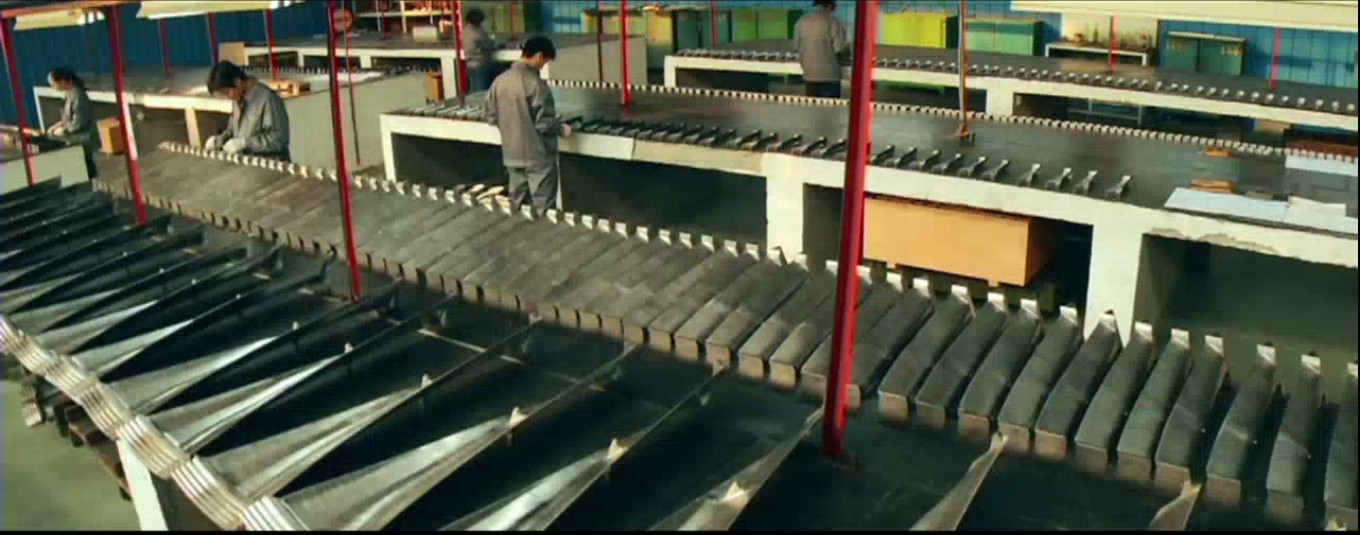
Packing and Delivery
After inspection, the completed vane products are packed and delivered to the customers. Depending on delivery schedules provided or required by the customers, the entire process from order receipt to final delivery ranges between three and eight months.
COMPANY
INFORMATION
BUSINESS
SOLUTIONS
